- 18
- South Africa
So I bought two TS-PC servo bases for chips, but they both have startup calibration issues, both start up and spin left to right a couple times, same fast speed both ways, and then tries to center, usually they miss the center, after which its back to spinning left and right. One of the bases has managed to finish calibration twice, after I fiddled with the Hall effect sensor, but seems like the calibration was off somehow, I then turned the wheel all the way clockwise and it rapidly spun all the way back counterclockwise, after which it seems the calibration was perfect, and FFB seems to work from the control panel . But when powering on the next time it struggles to calibrate again. It often times returns to dead center, but then starts spinning again...
I have read that the T300 sometimes has a issue where the rotor loosens from the shaft, but in those cases the spin in one direction is usually slower than the other? I also found that Angle Motor Calibration tool and tried to run it, but it does not seem to even detect the bases, does it only work on the T300? Any idea what the issue could be? Firmware and drivers are fine.
Also, does anyone know the significance of the line on the driving cog? I assume its supposed to be aligned with the steering wheel at center?
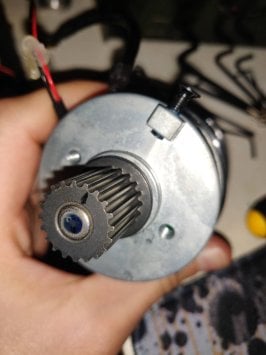
I have read that the T300 sometimes has a issue where the rotor loosens from the shaft, but in those cases the spin in one direction is usually slower than the other? I also found that Angle Motor Calibration tool and tried to run it, but it does not seem to even detect the bases, does it only work on the T300? Any idea what the issue could be? Firmware and drivers are fine.
Also, does anyone know the significance of the line on the driving cog? I assume its supposed to be aligned with the steering wheel at center?
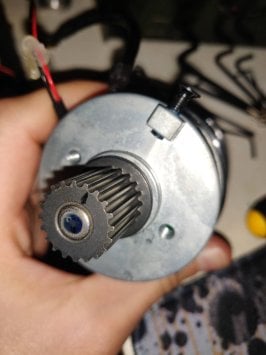